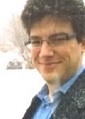
Marco G Rigamonti
Polytechnic University of Milan, Canada
Title: Vanadium pyrophosphate catalyst: Core-shell morphology and attrition resistance
Biography
Biography: Marco G Rigamonti
Abstract
Exothermic heterogeneous catalytic reactors are difficult to design when facing hotspots, radial and axial concentration and temperature gradients and run-away. Cylindrical pellets are the typical form for catalysts in fixed beds and the resulting long internal diffusion lengths limits the kinetics. Fluidized bed minimizes diffusional limitations with catalyst powders of 70 µm in diameter. Jet velocities on the order of 50 m s-1 mix the gas and solids thoroughly, resulting in high heat and mass transfer rates. However, the catalyst must withstand severe mechanical stresses induced by the jets. Creating attrition resistant porous micro-spheres is fundamental to compete economically with fixed bed reactor technology. Here, we synthesize vanadium pyrophosphate catalyst (VPP) as a template material to examine the effect of binders and spray drying conditions on attrition resistance and particle shape, size and porosity. A wet media mill (Netzsch mini-fer) ground commercial VPP precursor to a suspension of 7 µm and 0.5 µm primary particles in water. We tested several combinations of binders and additives including colloidal silica, polyvinyl alcohol, NaOH or H3PO4. A two fluid nozzle atomized the slurry inside a 0.8 m diameter drying chamber at 250ºC. EDS elemental mapping images demonstrate that the silica migrates to the surface during the drying process and forms a shell. Longer milling time achieves a smaller primary particle and the ASTM attrition test confirms a higher attrition resistance.